Mortar Colour - Coal Black
Interstar
#CM-015
Concentrated Mortar Colors. Interstar Mortar Colors are pure iron oxide mineral pigments designed to be used with all cementitious materials, including Type N, S, M or O strength masonry cement or Portland cement and lime mixtures. The pre measured units of Interstar Mortar Colors provide uniform color control with the flexibility of utilizing local masonry and/or Portland and lime cements to achieve the proper strength and mix design for brick, block stone unit construction. Interstar Mortar Colors are certified ASTM C979 for integral coloring. Size: 3 lb bag.
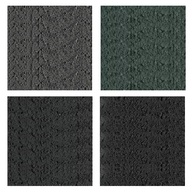
Mortar color has a dramatic affect on the outcome of masonry projects. Mortar color is no longer considered just a functional material - it is a design element that adds beauty and value to a home or building. Mortar color makes up approximately 20% of a wall surface, so selecting the right mortar color is critical. Interstar offers a wide spectrum of easy-to-use, vibrant, premium quality mortar colors made from iron oxide pigments to enhance brick, block and stone.
Interstar also offers custom blend mortar colors to that are tailored to the needs of our customers.
- INTERSTAR Pigment can be added to any concrete mix.
- INTERSTAR pigments are packaged in premeasured bags that disintegrate in the concrete for easy, clean use.
- Easy Dispersing
- Maximum coloring power
- Wide variety of vibrant colors
- Environmentally friendly and non-toxic
- Sunfast
- Lime-proof
Interstar Mortar Colors turn an ordinary project into something extraordinary. Use Interstar Mortar Colors to enhance the beauty of brick, block and stone by using a contrasting mortar color or a complimentary mortar color between masonry units and joints.
Mixing
- Step 1: The truck mixer drum must be completely clean with no leftover water or aggregate before mixing a batch of colored concrete.
- Step 2: The slump must range from 90 mm to 100 mm (3 1/2" to 4"). If air is entrained, it should range from 5% to 7%.
- Step 3: Put the drum in reverse (discharge) to shift the concrete toward the back of the drum and then stop the drum. Place the bags of pigment directly onto the concrete, then place the drum in forward (mix)
- Step 4: Let it turn slowly (5 rpm) for 2 or 3 minutes.
- Step 5: Then let the mixer run at optimum speed (12 rpm) for 10 to 15 minutes.
Caution: Never add extra water to a batch of colored concrete. Any differences in slump in successive batches will result in color variations in the concrete. Never use calcium chlorides or any accelerators.
Finishing
- Step 1: Place the concrete, then strike it off using recognized methods.
- Step 2: Once the concrete has been struck off, use a vibrating screed or a magnesium float. Take care to work in one direction.
- Step 3: Waiting period (do not allow the concrete to get too hard). Allow sufficient time for the concrete to set; rushing the other steps can alter the final appearance of the concrete.
- Step 4: Initial floating should be halted if there is any bleed water on the surface of the concrete (bleed water can result in scaling). Floating can be continued once the bleed water has evaporated. Stamping is the next step, if it is to be carried out.
- Step 5: A power trowel or magnesium hand float can be used for a smooth finish, but over-working the surface will cause discoloration.
Caution: Never fog the surface of the concrete with water; never wet the tools during use. The use of water will result in discoloration and may even damage the surface of the concrete.
Due to color variations of various types of printers, the mortar colors presented on this website offer only an approximation of the actual color. You should use this mortar color chart for a primary color selection only.
These pictures give an idea of the color that is produced by using 0.5, 1, 2, or 3 bags of pigment per cubic meter of concrete.
![]() |
![]() |
![]() |
![]() |
CM-015 0.5 | CM-015 1 | CM-015 2 | CM-015 3 |